Siemens Step 5 7.2
The core component of a well-designed system architecture With the SCADA system SIMATIC WinCC V7, Siemens offers an innovative, scalable process-visualization system with numerous high-performance functions for monitoring automated processes. Whether in a single-user system or a distributed multi-user system with redundant servers, the system offers complete functionality for all industries. S12 S11 S10 S9 T8 T9 T10 S8 S7 S6 S5 T5 T6 T7 S4 S3 S2 T3 T4 S1 T12 T2 Step 4: Retract arm Auto Ver 1 Hand Ver 2 & &?1 =A1.0 =A2.0 Transition 4: Part inserted E 7,3 &?1 Auto enable. General: The Service Pack 2 for STEP 5 is now available. This Service Pack can be used both for STEP 5 V7.15 and for STEP 5 V7.2 and higher. Siemens Industry Online Support.
First SIEMENS Programming tutorial More tutorials to come. Please let me know what you would want to see next! Thanks for watching. マニュアル『Working with STEP 7 V5.5,Getting Started』の実例を習熟されることをお勧めします。 これらの例は、トピック「STEP 7 によるプログラミング」への簡単な紹介となります。 必要な基本知識 本マニュアルを理解するには、自動化技術の全般的な知識が必要. Siemens Step 5 Version 7.2 Download Siemens Step 5. STEP 7 Basic Information. STEP 7 Reference Information After you have installed STEP 7, you will find the electronic manuals in the Start menu under Simatic Documentation or alternatively, you can order them from any Siemens sales center. 11/2001, Programming and Operating manual, C79000-G8576-C920-05, 6ES5998-0MA24.
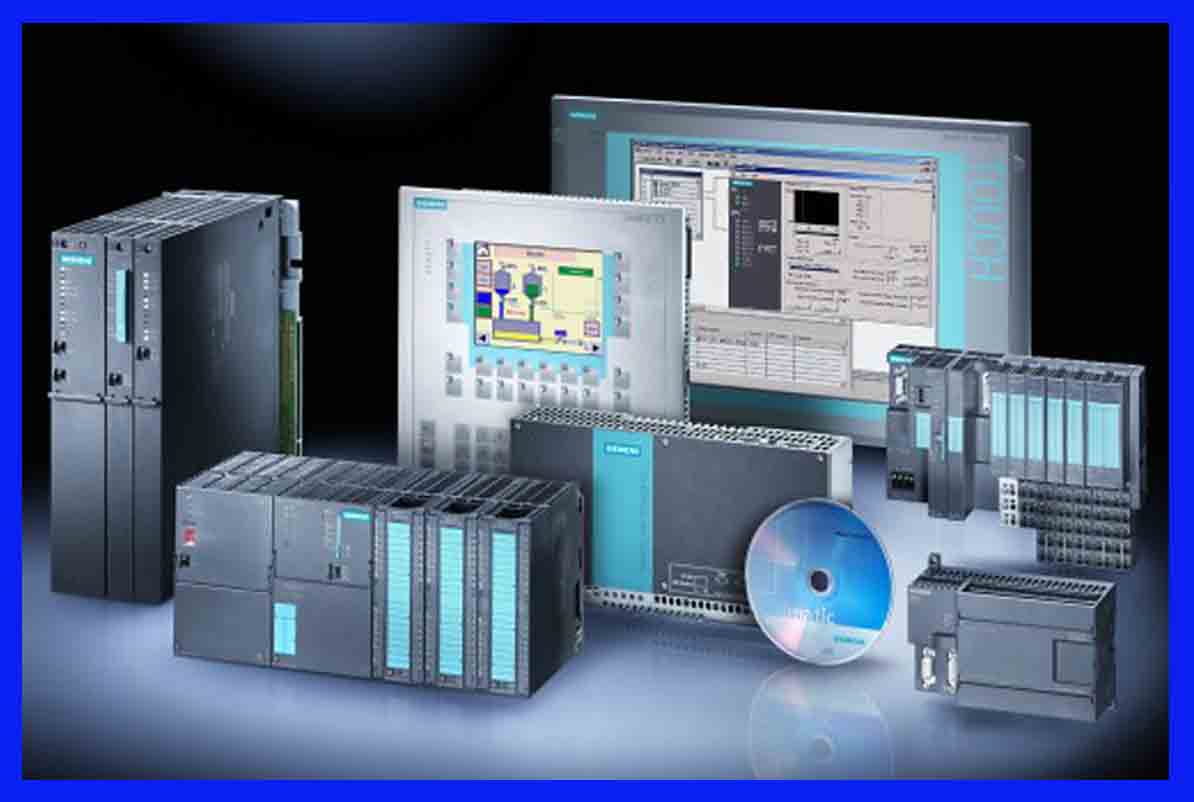
SIMATIC is a series of programmable logic controller and automation systems, developed by Siemens. Introduced in 1958, the series has gone through four major generations, the latest being the SIMATIC S7 generation. The series is intended for industrial automation and production.
The name SIMATIC is a registered trademark of Siemens. Dayz free download full game mac. It is a portmanteau of “Siemens” and “Automatic”.
Function[edit]
As with other programmable logic controllers,SIMATIC devices are intended to separate the control of a machine from the machine's direct operation,in a more lightweight and versatile manner than controls hard-wired for a specific machine. Early SIMATIC devices were transistor-based, intended to replace relays attached and customized to a specific machine. Microprocessors were introduced in 1973, allowing programssimilar to those on general-purpose digital computers to be stored and used for machine control.[1] SIMATIC devices have input and output modules to connect with controlled machines. The programs on the SIMATIC devices respond in real time to inputs from sensors on the controlled machines, and send output signals to actuators on the machines that direct their subsequent operation.
Depending on the device and its connection modules, signals may be a simple binary value ('high' or 'low') or more complex. For example, a binary input going from a thermometer on a machine to a SIMATIC device might have the following meanings:
- “High” signal: Temperature exceeded an operating limit
- “Low” signal: Temperature is within expected limits
Based on this input, and other factors, the program on the SIMATIC device might send a binary output signal to the same machine with the following meanings:
- “High” signal: Run the motor
- “Low” signal: Stop the motor
More complex inputs, outputs, and calculations were also supported as the SIMATIC line developed. For example, the SIMATIC 505 could handle floating point quantities and trigonometric functions.[2]
Product lines[edit]
Siemens has developed four product lines to date:
- 1958: SIMATIC Version G
- 1973: SIMATIC S3
- 1979: SIMATIC S5
- 1995: SIMATIC S7
SIMATIC S5[edit]
The S5 line was sold in 90U, 95U, 101U, 100U, 105, 110, 115,115U, 135U, and 155U chassis styles. The higher the number (except for the 101U), the more sophisticated and more expensive the system was. Within each chassis style, several CPUs were available, with varying speed, memory, and capabilities. Some systems provided redundant CPU operation for ultra-high-reliability control, as used in pharmaceuticalmanufacturing, for example.
Each chassis consisted of a power supply, and a backplane with slots for the addition of various option boards. Available options included serial and Ethernet communications, digital input and output cards, analog signal processing boards, counter cards, and other specialized interface and function modules.
SIMATIC S7[edit]
Siemens Step 5 7.2 Ft.
The first entries in the S7 line were released in 1994, available under three performance classes: S7-200, S7-300 and S7-400. The introduction of SIMATIC S7 saw also the release of a new fieldbus standard PROFIBUS, and the pioneer use of industrial Ethernet to facilitate communication between automation devices. The great success of the S7-300 CPU family in particular helped to cement the role of Siemens as one of the global leader in automation technology. These series are expected to be phased out in 2023.[3]
The first generation of S7 CPUs were later succeeded by the S7-1200 and S7-1500, released in 2012.[4] These models came with standard Profinet interface.
Software[edit]
Programs running on SIMATIC devices run in software environments created by Siemens. The environment varies by product line:
- The SIMATIC S5 product line is programmed in STEP 5.
- The SIMATIC S7 product line is programmed in STEP 7 (V5.x or TIA Portal).[5]
Step 5[edit]
The S5 product line was usually programmed with a PC based software programming tool called STEP 5. STEP 5 was used for programming, testing, and commissioning, and for documentation of programs for S5 PLCs.
The original STEP 5 versions ran on the CP/M operating system. Later versions ran on MS-DOS, and then versions of Windows through Windows XP. The final version of STEP 5 was version 7.2 (upgradable to version 7.23 Hotfix 1 with patches).
In addition to STEP 5, Siemens offered a proprietary State logic programming package called Graph5. Graph5 is a sequential programming language intended for use on machines that normally run through a series of discrete steps. It simulates a State machine on the S5 platform.
Several third-party programming environments were released for the S5. Most closely emulated STEP 5, some adding macros and other minor enhancements, others functioning drastically differently from STEP 5. One allowed STEP 5 programs to be cross-compiled to and from the C programming language and BASIC.
Structured programming[edit]
STEP 5 allowed the creation of structured or unstructured programming, from simple AND/OR operations up to complex subroutines. A STEP 5 program may, therefore, contain thousands of statements.
To maintain maximum transparency, STEP 5 offers a number of structuring facilities:
- Block technique - A linear operation sequence is divided into sections and packed into individual blocks.
- Segments - Within blocks, fine structuring is possible by programming subtasks in individual segments.
- Comments - Both a complete program as well as individual blocks or segments and individual statements can be directly provided with comments.
Methods of representation[edit]
STEP 5 programs can be represented in three different ways:
- Statement List (STL) - The program consists of a sequence of mnemonic codes of the commands executed one after another by the PLC.
- Ladder Diagram (LAD) - Graphical representation of the automation task with symbols of the circuit diagram
- Function Block Diagram (FBD) - Graphical representation of the automation task with symbols to DIN 40700/ DIN 40719.
Absolute or symbolic designations can be used for operands with all three methods of representation.
In LAD and FBD complex functions and function block calls can be entered via function keys. They are displayed on the screen as graphical symbols.
There are several program editors, from either genuine Siemens, or from other suppliers. After Siemens discontinued support, other suppliers started to develop new STEP 5 version which can run on Windows XP, or Windows 7.
Blocks[edit]
Five types of blocks are available:
- Organization blocks (OB) - for managing the control program
- Programming blocks (PB) - contain the control program structured according to functional or process-oriented characteristics
- Sequence blocks (SB) - for programming sequential controls
- Function blocks (FB) - contain frequently occurring and particularly complex program parts
- Data blocks (DB) - for storing data required for processing the control program.
Some S5 PLCs also have block types FX (Extended Function Blocks), and DX(Extended Data Blocks); these are not distinct block types, but rather are another set of available blocks due to the CPU having more memory and addressing space.
Operations[edit]
STEP 5 differentiates between three types of operations:
- Basic operations, (e.g. linking, saving, loading & transferring, counting, comparing, arithmetic operations, module operations) - These can be performed in all three representations.
- Supplementary operations and complex functions, (e.g. substitution statements, testing functions, word-by-word logic operations, decrement/increment and jump functions.) - These can only be executed in STL.
- System operations (direct access the operating system) - These can only be executed in STL.
Stuxnet[edit]
The Stuxnetcomputer worm specifically targets SIMATIC S7 PLCs via its STEP 7 programming environment.
Siemens Step 5 7.2 Cu.
References[edit]
- ^'60 Years of Simatic'. Siemens. Siemens. Retrieved 4 March 2020.
- ^'Siemens Simatic 505'. Computing History. Centre for Computing History. Retrieved 4 March 2020.
- ^'SIMATIC S7-300'. Siemens. Retrieved 12 November 2020.
- ^'What are the differences between SIMATIC S7-300 and S7-1500 PLCs?'. RealPars. Retrieved 12 November 2020.
- ^'PLC Programming with SIMATIC STEP'. Siemens. Siemens. Retrieved 4 March 2020.
External links[edit]
- Hans Berger (2009) [2000]. Automating with SIMATIC. ISBN978-3-89578-333-3.
- Hans Berger (2011). Automating with SIMATIC S7-1200. ISBN978-3-89578-356-2.
- Jürgen Müller (2005). Controlling with SIMATIC. ISBN978-3-89578-255-8.
Key Features
| Supported S5 PLCs
|
For extensive details on this product, please visit the product focus site.
If you are a current user that needs to upgrade, please call or email.
With S5 for Windows, existing programs can be edited directly without import/export. The logic presentation is available in Ladder Diagrams, Control System Flowchart, and Statement List. S5 for Windows® is compatible to the original Siemens programming unit. For automatic troubleshooting and simulation, the S5 Doctor functions are integrated as well.
All PLC online-functions are implemented. The new operational concept of version 6 has been developed on the basis of the newest cognitions in operator guidance. Block lists and symbolic tables for example can be arranged freely, they can be drawn in any order from the main window onto a second screen and can be faded out automatically from the main window, in order to gain more space on the screen. The presentation of the module parameters has been adjusted as well.
The S5 for Windows software product is an excellent software tool for creating, modifying, testing, and documenting programs for Programmable Logic Controllers (PLC). S5 for Windows is used to program the Siemens PLC family SIMATIC S5 with the programming language STEP 5. The logic presentation includes Control System Flowchart (CSF), Statement List (STL), Ladder Diagram (LAD) for programming, editing, and testing.
S5 programs can be edited directly without import/export. S5 for Windows® is compatible to the original Siemens programming unit. For automatic troubleshooting the S5 Doctor functions are integrated as well.
For the Siemens user with S5 PLCs and starting to use S7 PLCs, the S7 for Windows package that is available separately or bundled with S5 for Windows is an excellent choice. With the combination of S5 for Windows and S7 for Windows, you can easily convert your S5 programs to S7 programs.
Contents of this package
When you purchase this item you get the S5 for Windows package that provides the following programming options.
- Statement List (STL)
- Control System Flowchart (CFL)
- Ladder Diagram (LAD)
Also included in the package is a S5 PLC simulator application that runs on your PC and allows you to test your programs. Additionally, the S5 Doctor automatic troubleshooting functions have been integrated into version 6.
Siemens Step 5 7.2 Cu Ft
This package does not include a cable. This software can use the standard Siemens programming cables for your PLC. If you have an existing programming cable that you used with Step 5 it will work with this package. If you do not have a cable simply ask your local Siemens distributor for the cable used to connect the programming port on your specific model of S5 PLC to a computer RS-232 port.
Windows Platform Support
The user can select the Windows operating systems he or she prefers to use for programming. The software packages S5 for Windows® requires a 32-Bit Operating System and may be installed on
- Windows XP (32/64 Bit)
- Windows Vista (32/64 Bit)
- Windows 7 (32/64 Bit)
- Windows 8 (32/64 Bit)
Creating and Editing
A comfortable editor to create and edit symbolic tables is integrated. Searching and replacing for any criteria as well as rewiring is possible. A syntax check for already available addresses, symbolic or absolute, is integrated. The new comfortable multiple segment editor for the creation of statement lists, function block and ladder diagrams allows the representation of complex functions too.
Focus was set on the ease of use with the mouse and/or the keyboard. Cross references and/or the corresponding symbol files are shown with the correct addresses. In this window the symbol file can be edited simultaneously. The allocation of new addresses with syntax check is integrated. Statement lists are created with the comfort of integrated editor.
The Windows® clipboard can be used for program or configuration manipulations in any place. Statement lists can be altered into function block or ladder diagrams, as far as they can be displayed. The display of Function Block Diagrams and Ladder Diagrams in form of State Statement Lists is always possible.
Documentation
S5 for Windows® supports the installed Windows Printer. The program created will be printed with multiple comments and preset headers and footers. The selection of font and size are obvious. A separate dialog box is provided to select groups of operands to be printed as a Cross Reference list. Open windows, such as the status window, may also be printed.
S5 Simulator built in
With the Integrated Simulation PLC it is possible to test your S5 PLC programs. /download-yosemite-10105-dmg.html. No additional hardware is needed. The test will be performed on your PC. The Integrated Simulation PLC gives you the same online status display as a real PLC connected via a serial link. With the click of the mouse or with the keyboard you can set or reset Inputs, Outputs, or Flags directly within the online status display. From the Integrated Simulation PLC Window the PLC program can be executed in single steps. The single step operation allows you to execute a single program cycle, a single Block, or a single instruction within a block. You will find buttons to start, stop, and execute the start OB’s. Fields to display the value of variables (operands, timers, counters data words etc.) and fields to display and set inputs, outputs, and flags, are provided. The Integrated Simulation PLC is an open system. It is also possible to connect Peripheral Bytes with hardware ports. Doing so, the Integrated Simulation PLC may read or write to (I/O Boards) having hardware ports. To extend the instruction set, the Integrated Simulation PLC has the ability to call DLL programs whenever it executes an unknown command.
Siemens Step 5 7.23
Online Delivery - For customers who wish to receive this product without waiting for a CD to ship, electronic delivery is available. Online delivery of the install set is instant and your serial and PIN number for installation are delivered by email within 1 to 2 business days depending up on the time of day ordered. If you want us to also ship you a CD, please choose the physical delivery option - you can still request electronic delivery. NOTE that if you do not choose physical delivery at the time of order but later request that we ship a CD, additional charges will apply.